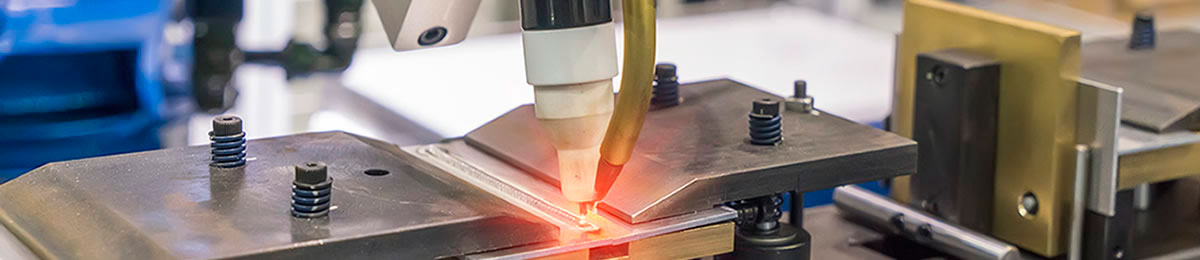
Procs
Industrial efficiency improvement
PROCS is a production control and traceability system, in charge of controlling the manufacturing flow of each part along the assembly lines.
Assists operators, validating each process step and ensuring it's produced quality. PROCS communicates with the industrial plant through different devices in the production line, such as PLC’s, robots, barcode readers, printers, computers and mobile devices like tablets and mobile phones.
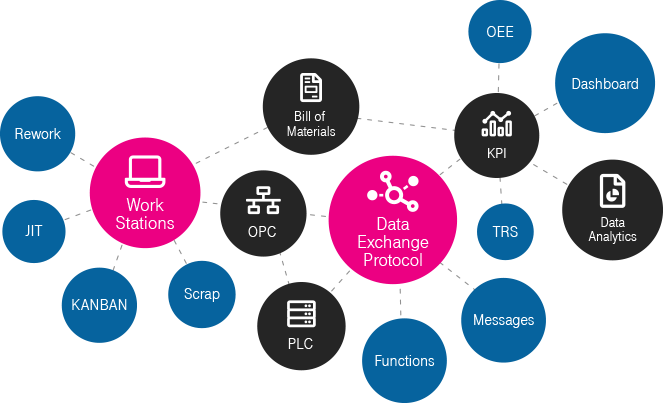
Production control
- Workstations and assembly lines management. Can be scaled to manage up to 300 workstations per server for larger installations.
- Productive workflow management and configuration (sequential and non sequential operations control, production routes).
- Discrete materials list's management in batch and semi-elaborated.
- Recipe and process parameters management.
- Production process quality assurance (component validation, POKA-YOKE, unique serial numbers in safety components, batches, machine processes and quality control operations).
- JIT mode production from automatic orders and in Kanban mode from manual orders.
- Mono and multi reference production control, using multiple positions and traceability tools.
- Production stations control
- Manual and automatic.
- Re-work and defects.
- Mono and multi reference packing.
- Batch production.
Traceability
- Operations performed on each part are recorded, storing
- Components (discrete, batches and semi-elaborated)
- Operators
- Process parameters sent to machine
- Used containers
- Machine tools
- Machine production process results and data.
- Rework operations log.
- Defect declaration and parts rejection log.
- Quality control log.
- JIT orders log.
- Historic data storage.
Part identification
- Label printing with part type and operation configurable content.
- Crystal Reports print engine for complex labels.
- ZPL printing engine and plain text formats for Zebra, Intermec and similar label printers.
- Working without labels is also possible, using component barcodes or RFID tags to identify parts.
Interaction with industrial devices
- Production line devices connectivity(PLCs, robots, barcode readers, printers, pick-to-light systems) using standard OPC, HTTP and TCP protocols and field protocols such as ModBus, AtlasCopco and Zebra.
- Real time operator's station web interface using industrial computers, tablets or other mobile devices.
- HMI devices connected to the PLC as operator interface.
- PLC’s exchange protocol with basic functions such as receiving components, sending process parameters and receiving results, as well as special functions such as validating user, user disconnection, batch reception, process cancellation and almost 100 functions more.
- Line device simulators (virtual devices) for modeling and validation purposes before commissioning (“virtual commissioning”).
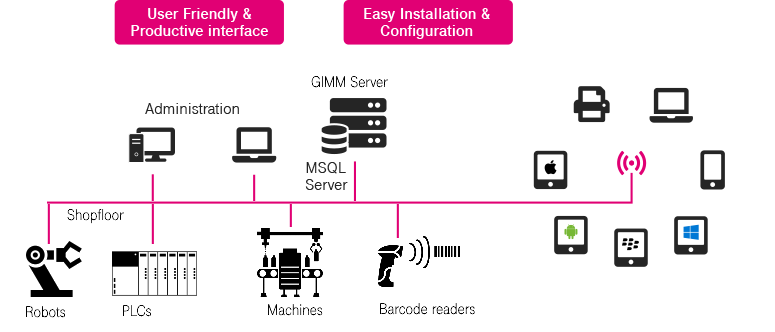
Monitoring
- Workstation supervision and connected industrial devices status.
- Production KPI's monitoring (OEE, Performance, Quality and Availability).
- Production alerts on screen, email, printed labels and orders to PLC’s.
- System errors and events log for production servers and connected industrial devices.
Data integration with other systems
- ERP's Master data import.
- Production declaration using HTTP REST protocols, file and database exchange.
- Traceability export to XML files.
Business Intelligence
- Real-time KPI's productivity reports.
- Traceability and production monitoring reports.
- Historical traceability data export for exploitation in BI systems.
Product shots